X-ray empty bottle inspector
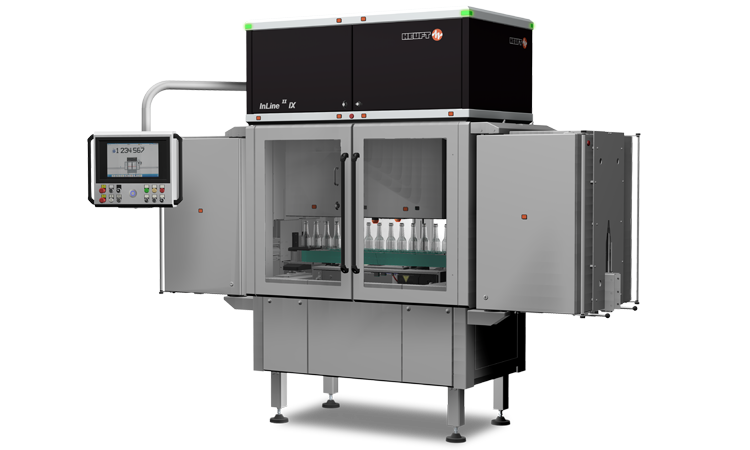
HEUFT InLine II IX
Detecting glass in glass and more: Smart all-surface empty bottle inspection with pulsed X-ray power.
Intelligent color sensor cameras developed in-house for complete optical inspection. Perfected pulsed X-rays for greater failure and detection reliability. The latest AI technologies for superior image analysis. And a cleaning and maintenance-optimized HEUFT CleanDesign: the HEUFT InLine II IX realizes full performance during the complete quality inspection of all areas of each individual empty bottle – and achieves a new level of precision not only in the challenging detection of glass-in-glass.
Infeed check
Ensure brand purity: Pre-sorting for greater line efficiency.
Defective, deviating, non-brand: the HEUFT InLine II IX can be equipped with various infeed check technologies – including a special rejection system which activates the most suitable rejection function depending on the problem bottle to be rejected – to prevent such bottles from coming in in the first place and impairing the performance of the inspection and the entire bottling line. Before the actual empty bottle inspection, this enables targeted pre-sorting for a single-variety infeed: only the correct empty containers, which can be inspected and filled without any problems, make it through. This not only ensures production quality, but also the efficiency and productivity of the entire line.
X-ray base inspection
Detecting simply more: Perfected pulsed X-rays.
We already developed the concept of using our unique X-ray flash technology for empty bottle inspection some time ago and have been continuously developing it ever since. It has long since established itself as the state of the art in the returnable and premium segment when it comes to reliably detecting glass splinters at the bottom of bottles, even in difficult cases. For example, if they are still surrounded by residual liquid from the washing machine. Compared to a purely optical inspection, pulsed X-rays increase the precision of glass-in-glass detection in such cases while minimizing the false rejection rate. Thanks to lifetime-optimized X-ray components and intelligent HEUFT reflexx A.I. X-ray image processing developed and manufactured in-house the new HEUFT InLine II IX achieves an unprecedented level of failure and detection reliability. Even during the identification of other high-density foreign objects, inclusions, shell-shaped fractures and cracks at the bottom of the empty bottle it is therefore simply much more effective!
Fullscreen
Intelligent optical base inspection
Gap-free examination: Full coverage at the bottom of the empty bottle.
Foil, cigarette butts, mould and other low-density foreign matter at the bottom of the bottle which could possibly escape the pulsed X-ray inspection are identified by the HEUFT InLine II IX with smart high-performance optics. HEUFT reflexx A.I. cameras from our own development and production in which our AI-supported image evaluation is directly integrated with the correct algorithms make such defects even more clearly recognizable. The same applies to scratches and cracks in the glass, among many other things. Flexibly controllable LEDs ensure homogeneous illumination of the entire bottle base – and therefore full coverage during optical base inspection. Regardless of their respective position, even transparent and reflective films can be reliably detected. HEUFT reflexx A.I.combines and analyzes the detection images in real-time, distinguishes harmless deviations such as drops of water smartly from critical defects and thus ensures even greater detection accuracy with a reduced false rejection rate.
Fullscreen
Finish and thread inspection
Finding defects and cracks: Safety around the bottle opening.
Defects, cracks, rust rings, contamination on the bottle finish and damage to the thread: the HEUFT InLine II IX has intelligent processes for optical finish and thread inspection in order to find such defects before they jeopardize product safety. Spectral lighting, smart image analysis and corresponding HEUFT reflexx A.I. camera technologies open up completely new possibilities. The complete inspection of the inside of the finish also covers the entire thread and underchip area. Critical defects such as overpressed finishes, thermal cracks or stress cracks, which can occur during bottle production in the glassworks or during storage, become visible when inspecting the neck finish sealing surface. Compared to the previous HEUFT standard, the resolution of the brilliant images is increased by a factor of four. This ensures the integrity of the area around the bottle opening as well as the sealability of the empty bottle to be filled.
Fullscreen
Quadruple sidewall inspection
Undistorted coverage about 360°: complete all-round inspection.
HEUFT reflexx A.I. cameras with four times the resolution are also used for the complete optical inspection of the side walls of each individual empty bottle, in which smart LED lighting is integrated as well as the AI-based image analysis. Critical defects such as transparent film and impurities in the empty bottle or inclusions, cracks and chips in the glass are thus made even more visible. The image resolution is now even eight times higher in the quadruple sidewall inspection, which covers well over 360 degrees of the bottle volume. Thanks to intelligent real-time image processing, the resulting detection images remain free of distortion. AI-based filters make cracks or inclusions in the glass visible even behind drops of water or embossing during real-time image evaluation and reliably distinguish them from non-critical objects. An optionally integrated special optic (see below) opens up unimagined perspectives during the smart side wall inspection of unfilled ACL bottles.
Residual liquid detection
Detecting caustic solutions, oils and paints: effective protection against product contamination.
Corrosive lye, oil or paint: even the smallest amounts of such residual liquids threaten the safety of the end product and the health of the consumer. The system uses two different methods to detect and remove affected empty bottles from circulation before they are filled: It uses high-frequency technology to identify residual suds and infrared sensors to identify oils and varnishes. Like all the detection modules of the completely redesigned HEUFTInLine II IX the HEUFT fluid units for residual liquid detection are fully integrated, safely enclosed and motor-adjustable. Thanks to the new construction of the X-ray supported empty bottle inspector in the hygiene-optimized HEUFT CleanDesign the compact module for detecting residual liquids now demonstrates its impressive precision directly in the device.
Fullscreen
Rejecting faulty products
Preventing recalls: reliable rejection of faulty containers.
Fast, already accurate: maximum precision during fault detection is only of any use if the affected products are subsequently removed from circulation. Single and multi-segment rejection systems from the HEUFT rejector series do this precisely and gently at the same time.
Fullscreen
Product monitoring and self-tests
Play it safe: Precise product tracking, regular self-tests.
Always know where a particular bottle is currently located: Every single one is tracked very precisely for this purpose. This ensures that none remains uninspected. The integrated reject verification system also checks whether every product identified as faulty is actually removed from circulation. Standardized self-test programs ensure that the detection performance is checked regularly. Thanks to more storage space and computing capacity the new HEUFT reflexx A.I. cameras now make even more possible in terms of self-monitoring.
Fullscreen
Easy changeovers
Automatic changeovers: Sustainable reduction in set-up times.
For a seamless complete inspection, servo technology on the cleverly driven conveyor not only realizes a targeted rotation and precise fine alignment of each individual bottle. It also adapts the height and width of the conveyor belt precisely to the changed format when changing types. The same applies to the positioning of all detections. Thanks to clearly reproducible type settings, this is done completely automatically. This reduces the need for manual intervention, saves personnel resources and not only saves time, but also money: efficiency and productivity losses due to lengthy changeover times are sustainably reduced.
Optional additional functions
Detect even more: Expanding the range of functions.
HEUFT SPECTRUM II systems have a modular design and can be extended at any time. A scuffing detection system can be integrated into the HEUFT InLine II IX as an option, particularly for returnable packaging machines. Combined with a rejection rate control system, less heavily scuffed bottles are only rejected if the production situation particularly allows it. The sidewall inspection of ACL bottles now not only verifies the presence of Applied Color or Applied Ceramic labels. With AI-based filters from the HEUFT reflexx A.I. image processing system they can even be hidden for a truly complete inspection in order to find hidden defects.
read more...
A special optic which can be integrated as an option now even enables the detailed inspection of the ACLs themselves so that, for example, misprints or markings, logos and colorations which do not match the type being used can be reliably identified. It can also be retrofitted at any time: a separate recognition unit for the verification of DataMatrix and QR codes on the bottle wall in particular. The HEUFT InLine II IX also offers various options for neck finish inspection - from color ring inspection of the sealing surface to ovality detection. And in addition to those already integrated in the device, further modules for residual liquid detection can be mounted on the conveyor for redundant protection. Real system technology!
寿命优化脉冲 X 射线
更好、更持久的检测: 技术独特,可靠性更高
更精确、更温和、更耐用:HEUFT X 射线系统的独特之处首先在于我们独有的脉冲 X 射线技术。我们只发射毫秒级的 X 射线脉冲,而不是不间断的连续光束。而且,只有当需要检测的产品实际处于检测区域时,才会发出X射线脉冲,以检测是否存在危险异物和其他安全隐患。即使生产线速度极高或波动较大,也能以无与伦比的低辐射实现全面可靠的检测。专门开发的 X 射线管和其他经过持续优化的部件不仅提高了辐射检测的覆盖范围和灵敏度,还提高了可靠性和使用寿命。在可靠性和使用寿命方面也是如此,从而大大降低了总体拥有成本(TCO)
更多信息...
在单个 X 射线组件失去性能或出现故障之前,我们会及时通知用户,以便他们有足够的时间进行预防性维护。灯丝甚至是冗余集成的:如果一个灯丝出现故障,另一个灯丝会立即全自动接替,这样生产就不会中断。此外,HEUFT 的新型全场图像转换器现在可以在现有维护合同框架内保证八年的使用寿命,并且在此期间出现故障时可以免费更换,从而确保了更高的灵敏度、可用性和运行可靠性,并降低了总体拥有成本。
Fullscreen
HEUFT SPECTRUM II
简单自动化:性能最大化的通用设备平台。
高度自动化、通用和强大:HEUFT SPECTRUM II能够确保在线检测过程中最优化的检测和可靠的操作,以持续保障产品质量和生产线效率。高度自动化及多重处理能力的跨系统控制单元用于不同模块、系统和应用。无需人工干预就可以进行瓶型和结构更换。通用平台独一无二的人机界面是不言自明的,有效地节约了人力资源。内部研发的新一代硬件和软件以及具有前瞻性的网络连接能够达到最大的计算机处理能力和实时数据传输。结论就是:有目的地产品追踪、检测和剔除过程中能达到最大精度。
Fullscreen
HEUFT reflexx A.I.
只需识别更多: 人工智能实时图像处理。
自 2010 年以来,我们自主开发的图像处理技术已经掌握了用于目标对象分类的机器学习这一人工智能学科!从那时起,它已经学会了很多:智能过滤器可以区分容器上的水滴和玻璃中的气泡,甚至可以识别隐藏在 ACL 或浮雕后面的微小缺陷。HEUFT reflexx A.I. 现在还使用了深度学习技术!
经过适当训练的神经网络可用于去噪 X 射线图像或在结构化产品中发现危险异物,并将其与形状、大小和密度极其相似的良好物体可靠地区分开来。通过真正的人工智能,我们自主研发和生产的硬件和软件再次提高了检测的可靠性,并将错误剔除率降至最低。智能图像处理可直接集成到 HEUFT reflexx A.I. 相机中,该相机由公司内部开发,可直接实时处理和评估自身图像,并将自适应图像分析提升到最高水平。
Fullscreen
HEUFT NaVi
轻松知道该怎么做:不言自明的试听用户指南。
直观、独特和试听:无需为了可靠操作HEUFT SPECTRUM II系统而实现学习。HEUFT NaVi用户指南是不言自明的,能够分别一步步地支持用户。带有用户相关权限的RFID登录系统提供了一个概述,使得每个用户的工作都变得简单轻松:用于能在清晰排版的触摸屏用户界面上看到他真正所需要的,通过一个平面菜单结构,综合的教程和精确的辅助工具以最佳的满足他的要求。在这个过程中,他将受到虚拟助理的支持。她会与其说话,并详细地跟他说明何时何地做什么。有目的地关注重点:试听的HEUFT NaVi用户指南使得可靠地操作HEUFT系统变得轻松简单!
Fullscreen
HEUFT checkPoints
简单地查看哪里需要做什么:无故障定位。
清晰、直接和有目的性:用户可以在需要人工干预的情况下立即处理这一罕见情况。因为除了HEUFT NaVi提供的试听信息,醒目的HEUFT checkPoints一下便能马上清晰准确地判断何时必须着手采取行动。万一出现最糟的情况,橙色标签不仅在触摸屏上,同时也在各个部件上闪烁。它的位置不需要长时间搜索。这节省了人力资源,缩短了停机时间从而增加了生产力。
网络技术
全面联网:在线连接以提高效率和质量。
信息实时传输,生产数据采集,线路分析和远程维护:联网就是答案!HEUFT系统拥有前瞻性的网络界面(千兆以太网和TCP / IP)用于通过网络和数据库界面(SQL / DDE)进行在线连接,以通过非常快速和简单的工作流程达到最高的生产线效率和最优的质量管理。因此,可实现全网络可用生产数据、交班记录、生产力错误和HACCP限值分析。结论是:尽早发现质量及效率问题。防火墙能保护与HEUFT TeleService的直接连接以实现全天候提供可靠的远程服务。
HEUFT CleanDesign
清洁相当简便:卫生优化建设。
方便、清洁和安全:HEUFT CleanDesign系统指定用于卫生敏感区域。倾斜的表面有利于清洁和防止顽固污垢积累。特殊的通道和开口允许用于清洁所需的液体完全排干。因此,无论如何危险的病菌和细菌都不接触表面。特别设计的外壳和门板方便打开。电子产品完全封装。一些敏感的区域如检验单元都能防尘、防接触以及防喷水。
Fullscreen
HEUFT rejector
剔除错误的产品:适合所有箱子的剔除器。
The compact HEUFT flip and HEUFT mono single-segment systems as well as the HEUFT DELTA-K and HEUFT DELTA-FW multi-segment rejectors are ideally suited for the reliable discharge of faulty full products.-
reliable detection of glass-in-glass and other foreign objects of high and low density
-
gapless inspection of all surfaces of empty bottles
-
unique combination of intelligent high-preformance optics and exclusive X-ray flash technology for full detection and rejection reliability
-
high-resolution color sensor camera images
-
brilliant X-ray shots with minimal radiation
-
AI-supported camera and X-ray image processing with HEUFT reflexx A.I.
-
revised HEUFT CleanDesign for better accessibility for cleaning and maintenance
-
highly automated HEUFT SPECTRUM II platform with self-explanatory HEUFT NaVi user guidance
-
automatic changes of type and format
-
easy integration into existing filling lines
-
online connection for remote maintenance and production data acquisition
-
Output range: up to 72,000 empty bottles / h
-
≤ 0.2 percent false rejection rate